A modern, ambitious project that unites ecology with high technology
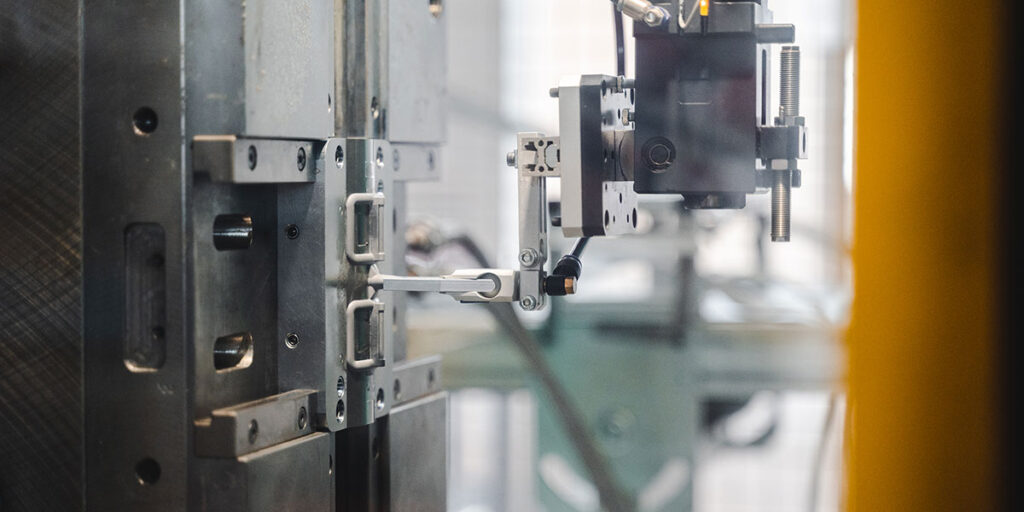
Metal Injection Moulding (MIM) is linked to a modern, ambitious project that has seen the Euro Stampaggi Group become one of the first companies in central Italy to put this sophisticated technology into production and to make it available to customers. This has been done as part of a programme of research and experimentation launched in the early 2000s with the School of Engineering at the University of Florence and with the Fraunhofer Institute in Bremen in partnership with the Florence-based company, Leo France.
Metal Injection Moulding comes from combining the injection moulding of plastic materials with the sintering of metal powders; a union that allows the utmost freedom in the study of new geometries without compromising the high productivity levels required nowadays by the market.
MIM technology makes it possible to obtain metal components of considerable geometric complexity and of small dimensions. Then there is the lower environmental impact to consider since no hazardous substances are used and any production waste can be completely reused.
The two companies in the Euro Stampaggi Group focused on this specific technology can, today, count on four production lines with complex, versatile machinery capable of making pieces that range from the tiniest dimensions to pieces weighing 80 grammes.